Proactive maintenance is a preventive maintenance strategy for stabilizing the reliability of machines or equipment. It has two parts:
- Preventive maintenance
- Predictive maintenance
A proactive maintenance gives a company the ability to prolong the life of machinery and prevent a complete and unexpected breakdown. Keeping the machines in a good condition by using high quality spare parts as well as consumables like filter elements and lubrication, improves the performance and productivity and reduces the downtimes and life cycle costs.
Proactive maintenance may look more expensive in the beginning, but these investments will pay back many times in view of the costs savings and reduction of downtimes over the long run.
The primary goal of Preventive maintenance is to avoid or mitigate the consequences of failure of equipment. It is designed to preserve and restore equipment reliability by replacing worn components before they actually fail. Preventive maintenance activities include partial or complete overhauls at specified periods, oil changes, lubrication, minor adjustments, and so on. In addition, workers can record equipment deterioration so they know to replace or repair worn parts before they cause system failure. The ideal preventive maintenance program would prevent all equipment failure before it occurs.
Predictive maintenance (PdM) techniques are designed to help determine the condition of in-service equipment in order to predict when maintenance should be performed. This approach promises cost savings over routine or time-based preventive maintenance, because tasks are performed only when warranted.
Preventive maintenance starts with a visual check of the machine, filter status and oil level every day and goes over to the improvement and monitoring of the consumables like filters and grease.
Using monitoring instruments like gauges or sensors can improve the control of the condition and allows a replacement when needed.
This means that the changing intervals can be extended if the filter and the oil are in good condition, but it also helps to identify bad condition which could lead to a damage and can be avoided due to the monitoring.
Special Filters can clean the fuel or the oil and therefore protect the internal systems of the machines from damages. Dirty fuel (particles and water) can damage the injection system and lead to a total breakdown, water and particles in oil can damage the pumps, hoses, sensors and also lead to a total breakdown. If a hydraulic oil is cleaned regularly, the lifetime of the oil can be extended up to 10 times and the lifetime of the hydraulic pumps can be increased from. e.G. 8.000 hours up to 25.000 hours.
Using complex or over-based grease, can extend the grease life time up to 4 times and also improve the adhesion and the EP performance. Calcium Sulfonate Over-base Grease have a very good water and corrosion protection as additional advantage.
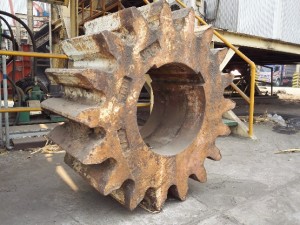
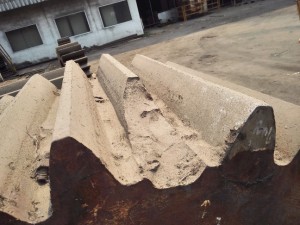
Damaged Gears after insufficient greasing and insufficient water protection
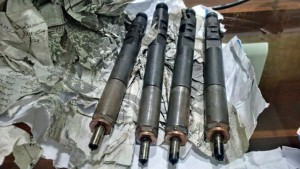
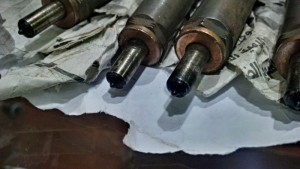
Damaged Injectors after running with highly contaminated diesel fuel